Durability Study Of Plastic Wood Composites
Wood-plastic composites are made by mixing low-melting thermoplastics with fiber materials such as wood powder and rice bran.It has the advantages of both plastic and fiber materials. However, it has the disadvantages of both materials:Plastics are prone to aging and degradation, and fiber materials are prone to absorbing moisture and decaying. At present, many plastic-wood composite products are widely used outdoors, so the study of durability properties such as aging and decay of plastic-wood composite materials is of great significance. Since the study of durability performance involves the analysis of the original properties of wood-plastic composites, the raw materials used to manufacture wood-plastic composites were first analyzed.
This paper focuses on the changing characteristics of wood-plastic composite materials under natural climate conditions. The changes in weight and macroscopic mechanical properties after being placed outdoors were analyzed.Four high-tech methods including Fourier transform infrared analyzer, differential scanning calorimeter, dynamic mechanical thermal analyzer and scanning electron microscope were used to track and detect the changing characteristics of the properties of plastic-wood composite materials.The results show that the endothermic peak appearing at around 60°C is mainly caused by the desorption endotherm of physically adsorbed water of cellulose in rice bran. The melting point of HDPE in the material is 126°C. The alternating effect of environmental factors will accelerate the breakage of molecular chains at the interface between rice bran and polyethylene and in the material matrix, reducing the internal friction at the α relaxation point. A large number of fine cracks on the surface of the material lead to a decrease in material performance.
Under laboratory conditions, the effects of various environmental factors (moisture, seawater, acid rain, fungi, ultraviolet light) were simulated, and the following conclusions were drawn:
(1) Under artificial simulated moisture conditions: the dimensional changes of the plate in different directions are: width direction > thickness direction > length direction;When the processing time is roughly the same, the average values of the ratios in different directions under different conditions are approximately: width/length=2.31, thickness/length=1.87, width/thickness=1.34.
(2) Under artificial simulation conditions, the macroscopic mechanical properties of the material have declined. The weight of the specimens increased under simulated seawater conditions. At the same time, the increase in the wood specimens was much higher than that of WPC, which was about 17 times that of WPC. Under simulated acid rain conditions, the stronger the acidity, the greater the impact on material properties. Under simulated fungus conditions, the weight of the wood-plastic composite material increased after decay, and the weight increase rate was approximately 0.78%. Under simulated conditions where ultraviolet rays and water interact together, the deformation vibration absorption peak and C=O stretching vibration absorption peak of methylene-CH2 increase more dramatically than under natural climate conditions, indicating that ultraviolet rays are extremely destructive to materials.
Relatest Post
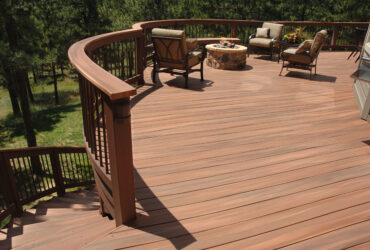
Common Structure Types In Wood Plastic Composite Material garden engineering
Details icon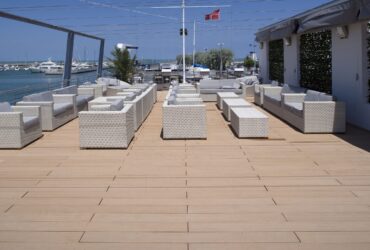